Sanitary grade automatic unpacking machine, capable of unmanned closed feeding, helps enterprises approach the
Date:2022/9/15
With the aggravation of China's aging, the disappearance of the demographic dividend, and the rapid rise of labor costs, various industries are facing the industrial upgrading led by intelligent manufacturing. As the demonstrator of intelligent manufacturing, lighthouse factory represents the highest level of Intelligent Manufacturing in the world. There are 103 lighthouse factories in the world, while there are 37 in China, covering many industries such as medicine, food and daily chemicals.
But the overall intelligent level of China's pharmaceutical, food, daily chemical and other industries is still in the primary stage, and many processes are not even automated. In terms of production and feeding, many enterprises still use manual handling, which greatly limits the intelligent development of the industry. With the successful listing of miran sanitary automatic bag unpacking machine, it provides an opportunity for the enterprise to fundamentally change the feeding mode, and also helps the enterprise to move closer to the "lighthouse factory".
Figure 1: Miran sanitary grade automatic bag unpacking machine
01 Sanitary grade automatic unpacking machine: specialized in solving feeding problems in pharmaceutical, food and daily chemical industries
The sanitary automatic unpacking machine researched and developed by our company is an automatic unpacking and feeding equipment integrating material conveying, bag breaking feeding, waste bag collection, dust removal system, etc. Focus on solving the problems of large demand, large handling labor, large feeding dust, low production efficiency and discontinuous production of production line in the production feeding of pharmaceutical, food, daily chemical and other enterprises. It is applicable to bag breaking feeding of powdery or granular materials, and different forms of packaging such as single-layer and double-layer packaging bags, woven bags and PE bags. The equipment can automatically detect incoming materials and complete automatic feeding, so as to achieve intelligent operation, greatly improve production efficiency, reduce labor intensity, reduce dust pollution, reduce feeding safety hazards, and avoid the impact of unpacked feeding of toxic materials on occupational health of personnel, etc.
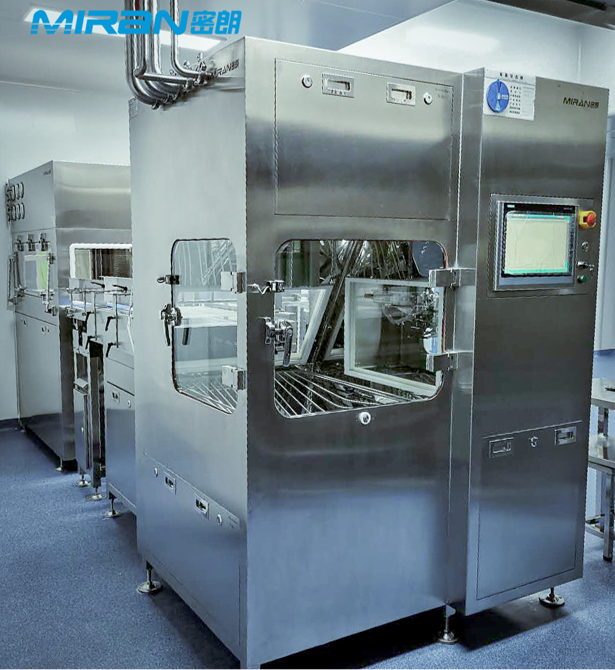
Figure2 : Miran sanitary grade automatic bag unpacking machine
02 Fully automatic feeding overall solution: can save a lot of operating costs for enterprises every year
The sanitary grade automatic unpacking machine can also integrate with our other intelligent equipment to provide a fully automated feeding overall solution. The entire feeding process can achieve completely unmanned production and continuous operation, effectively saving various operating costs for enterprises.
Figure 3 : Miran fully automatic feeding overall solution production line
Our fully automatic feeding overall solution is to grab the materials from the pallet to the conveyor belt through the depalletizing robot with identification system, and then identify and review the information on the external package through the information scanning identification system; Then, the external package of the materials is removed with the assistance of the outsourcing mechanism, and the materials are sent to the clean area after air shower disinfection. Then, the materials are checked by the weight scale and the cumulative feeding weight reaches the critical step. The automatic unpacking machine is used for unpacking and feeding. Then, the materials are weighed by the crushing or sieving machine, the vacuum feeder to the silo, and the vibrating feeder to match the platform scale, so as to connect the materials with the RGV IBC bucket and complete the whole intelligent feeding process.
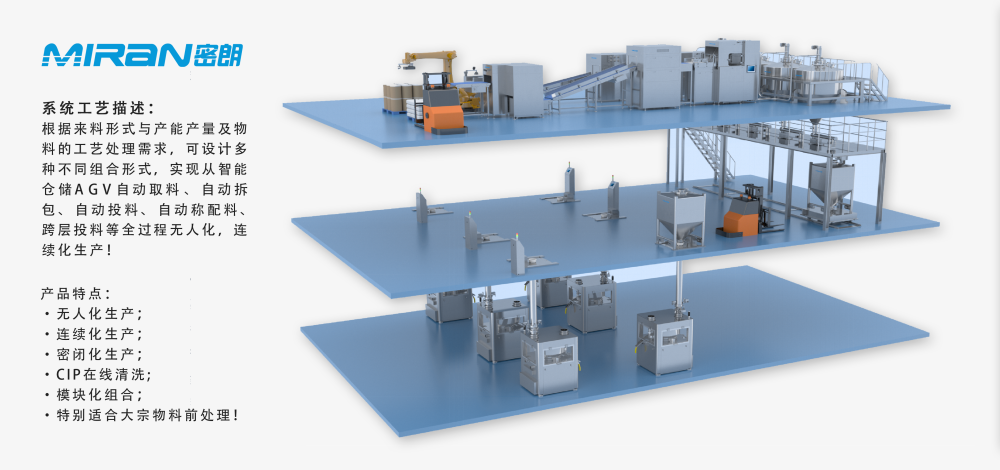
Figure 4 : Application model of Miran fully automatic feeding overall solution
03 Sanitary grade automatic unpacking machine replaces manual feeding: eliminating enterprise safety accidents and bidding farewell to labor shortage
Choosing a sanitary grade fully automatic feeding method can help enterprises avoid a series of risks. For example, a biotechnology company in Shandong once had a fire accident that caused multiple deaths and injuries. The cause of the accident was that the manual feeding staff did not strictly follow the work process due to personal issues, resulting in inaccurate handover information and repeated catalyst input. During the manual feeding process, it is inevitable that raw materials will be scattered on the entire workshop floor. If not treated promptly and thoroughly, there may be a risk of cross contamination of the products.
Choosing a fully automatic feeding method will fundamentally eliminate the above risks. The equipment can scan and identify materials to prevent errors; On the other hand, the entire process is carried out in a closed environment, combined with CIP online cleaning function, to avoid cross risks in drug production.
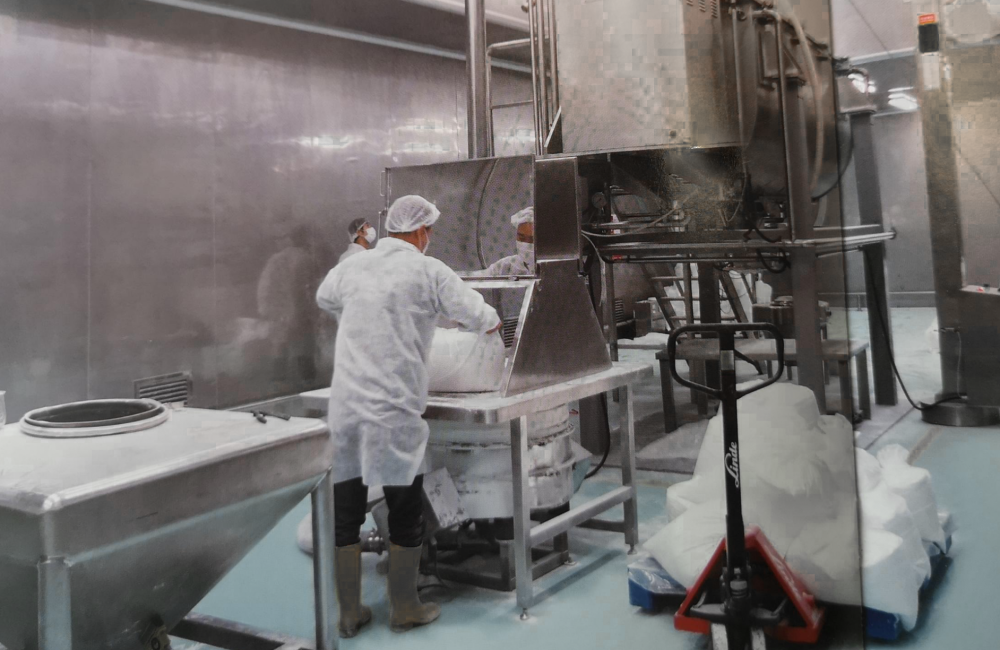
Figure 5 : Manual feeding site of a certain enterprise
For enterprises with large demand for products such as food and daily chemical industries and low added value, it is more necessary to use full-automatic unpacking machines for feeding and upgrading, so as to reduce labor costs and significantly improve production efficiency. It is the so-called "if you want to do a good job, you must first use your tools". Because of the high labor intensity and dust of manual feeding, it is easy to lead to high employee mobility and labor shortage, thus increasing the cost of personnel recruitment, training and human resource management.
Nowadays, the pharmaceutical, food, daily chemical and other industries are faced with a high degree of product homogenization and serious industrial entanglement. Intelligent manufacturing is undoubtedly an effective way for enterprises to maintain their core competitiveness and promote sustainable development; It is a powerful magic weapon to improve efficiency, reduce costs and quickly respond to user needs. It is understood that 82% of the lighthouse factories have significantly improved their production efficiency, and 66% of the lighthouse factories have improved their sustainability by reducing consumption, resource waste and carbon emissions. Although unpacking and feeding is only a link in the product production process, as the source process of manufacturing, intelligent feeding is of great significance for enterprises to realize intelligent manufacturing.